Vysoce krouticí mikro 35mm krokový motor pro tiskárnu
Popis
Existují dva způsoby navíjení krokových motorů: bipolární a unipolární.
1. Bipolární motory
Naše bipolární motory mají obvykle pouze dvě fáze, fázi A a fázi B, a každá fáze má dva výstupní vodiče se samostatným vinutím. Mezi těmito dvěma fázemi není žádné spojení. Bipolární motory mají 4 výstupní vodiče.
2. Unipolární motory
Naše unipolární motory mají obecně čtyři fáze. Na základě dvou fází bipolárních motorů se přidávají dva společné vodiče.
Pokud jsou společné vodiče spojeny dohromady, výstupní vodiče mají 5 vodičů.
Pokud nejsou společné vodiče propojeny, výstupní vodiče mají 6 vodičů.
Unipolární motor má 5 nebo 6 výstupních vodičů.
Parametry
Napětí | 8DV DC |
Počet fází | 4 fáze |
Úhel kroku | 7,5°±7 % |
Odpor vinutí (25 ℃) | 16Ω±10% |
Aktuální fáze | 0,5 A |
Aretační moment | ≤110 g/cm |
Maximální rychlost vtahování | 400 PPS |
Přídržný moment | 450 g/cm |
Teplota vinutí | ≤85 tisíc |
Dielektrická síla | 600 V AC 1 s 1 mA |
Návrhový výkres
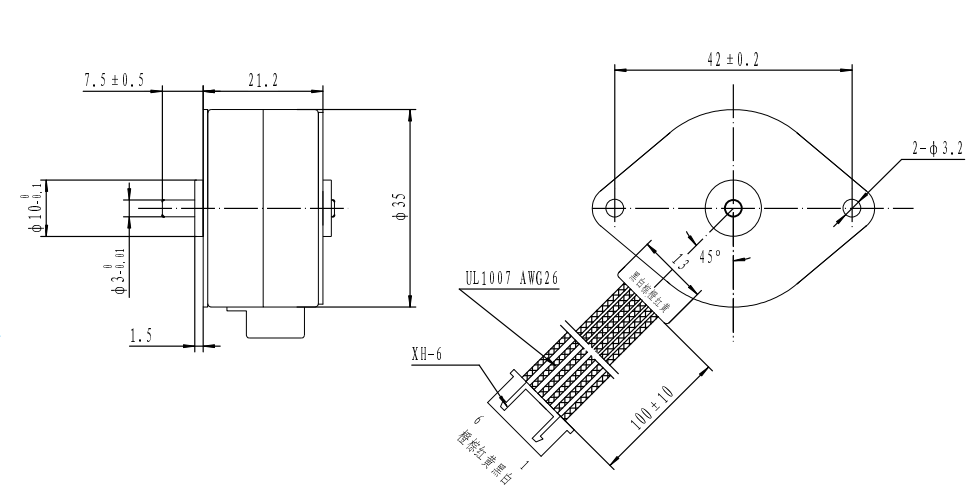
O základní struktuře krokového motoru s permanentními magnety
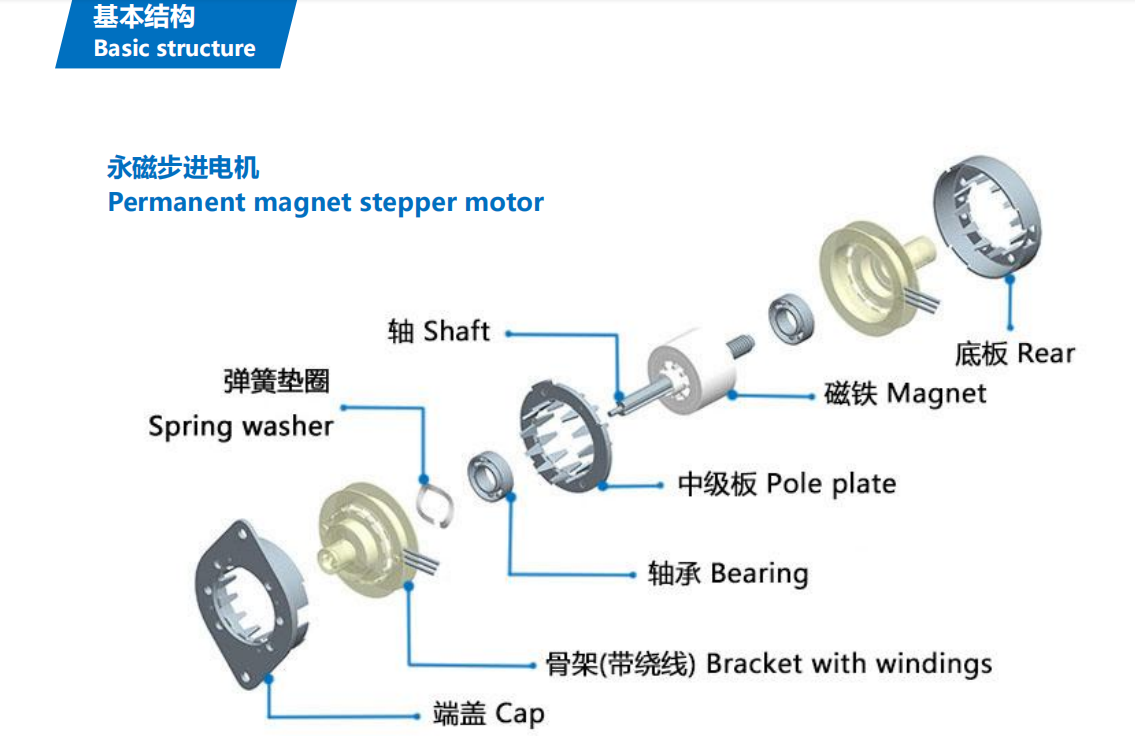
Vlastnosti a výhody
1. Vysoce přesné polohování
Protože se krokové motory pohybují v přesných opakovatelných krocích, vynikají v aplikacích vyžadujících přesnost
polohování, počtem kroků, o které se motor pohybuje
2. Vysoce přesné řízení rychlosti
Přesné kroky pohybu také umožňují vynikající kontrolu nad rychlostí otáčení pro daný proces
automatizace a robotika. Rychlost otáčení je určena frekvencí pulzů.
3. Funkce pauzy a podržení
Při řízení pohonu má motor funkci blokování (vinutími motoru protéká proud, ale
motor se neotáčí) a stále je zde výstupní přídržný moment.
4. Dlouhá životnost a nízké elektromagnetické rušení
Krokový motor nemá kartáče a nemusí být komutován kartáči jako kartáčový motor.
Stejnosměrný motor. Nedochází k žádnému tření kartáčů, což prodlužuje životnost, nedochází k elektrickým jiskrám a snižuje se elektromagnetické rušení.
Použití krokového motoru s permanentním magnetem
Tiskárna
Textilní stroje
Průmyslové řízení
Klimatizace
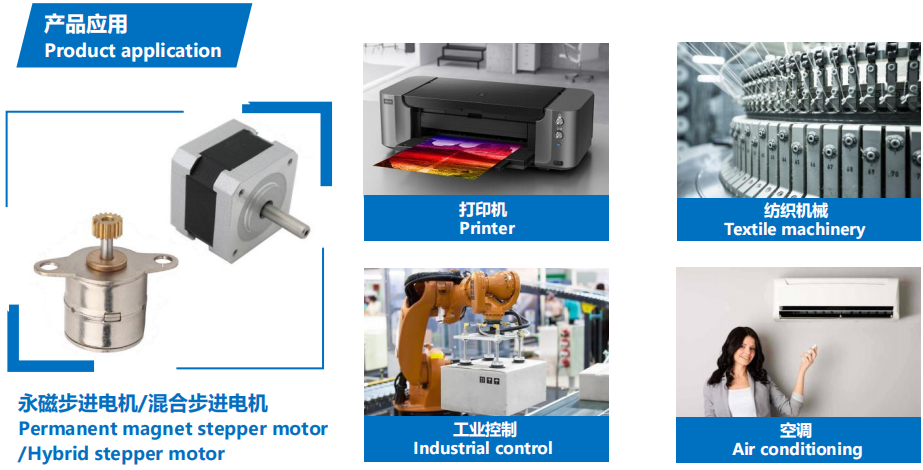
Princip činnosti krokového motoru
Pohon krokového motoru je řízen softwarem. Když se motor potřebuje otáčet, pohon se
aplikujte impulsy krokového motoru. Tyto impulsy napájejí krokové motory v určeném pořadí, čímž
způsobení otáčení rotoru motoru ve specifickém směru (ve směru nebo proti směru hodinových ručiček). Tak, aby
dosáhnout správné rotace motoru. Pokaždé, když motor obdrží impuls z budiče, otočí se o úhel kroku (u pohonu s plným krokem) a úhel natočení motoru je určen počtem vyvolaných impulsů a úhlem kroku.
Dodací lhůta a informace o balení
Dodací lhůta pro vzorky:
Standardní motory skladem: do 3 dnů
Standardní motory nejsou skladem: do 15 dnů
Produkty na míru: Přibližně 25~30 dní (v závislosti na složitosti přizpůsobení)
Dodací lhůta pro výrobu nové formy: obvykle asi 45 dní
Dodací lhůta pro hromadnou výrobu: na základě množství objednávky
Obal:
Vzorky jsou baleny v pěnové houbě s papírovou krabicí a odesílány expresní zásilkou.
Hromadná výroba, motory jsou baleny do vlnitých kartonů s průhlednou fólií vně. (doprava letecky)
V případě přepravy po moři bude produkt balen na paletách.
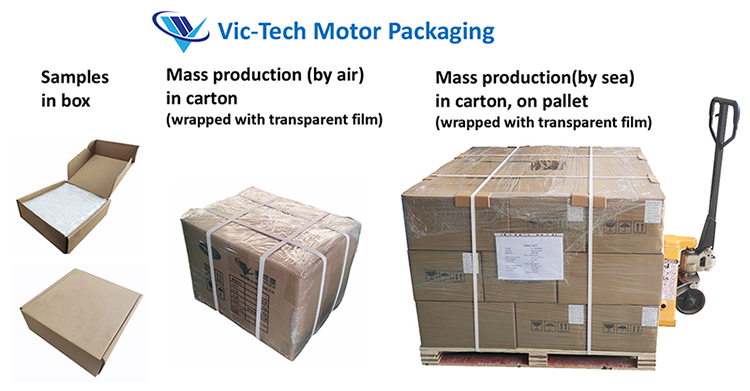
Způsob platby a platební podmínky
Pro vzorky obecně přijímáme Paypal nebo Alibaba.
Pro hromadnou výrobu přijímáme platby T/T.
U vzorků vybíráme plnou platbu před výrobou.
Pro hromadnou výrobu můžeme přijmout 50% platbu předem před zahájením výroby a zbývajících 50% platby uhradit před odesláním.
Poté, co budeme spolupracovat na objednávce více než 6krát, můžeme vyjednat další platební podmínky, jako například A/S (po vidění)